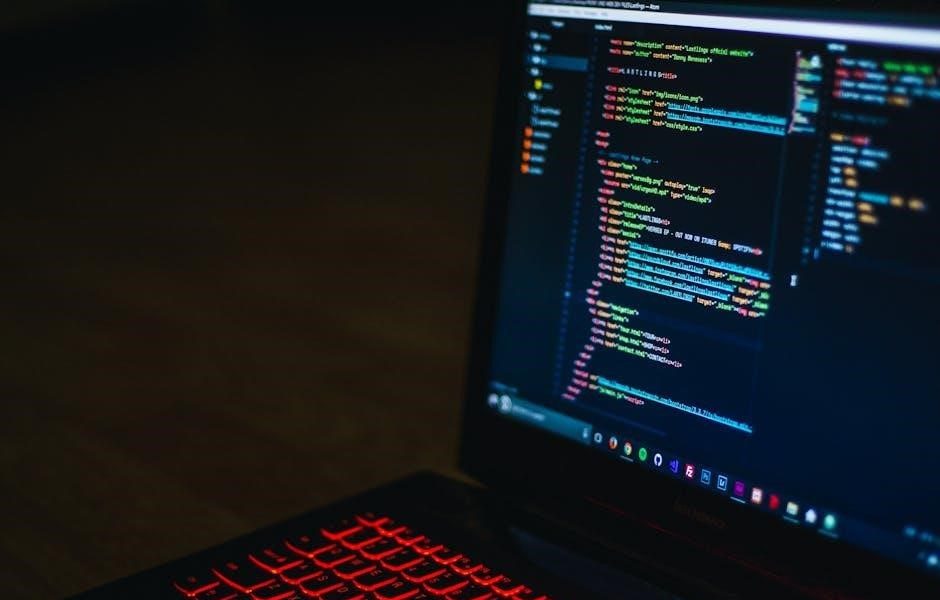
powerflex 753 programming manual
Welcome to the PowerFlex 753 Programming Manual‚ a comprehensive guide designed to help users effectively program and operate the PowerFlex 753 AC drive. This manual provides detailed instructions‚ configuration tips‚ and troubleshooting strategies to ensure optimal performance and safe operation of the drive. It is an essential resource for engineers‚ technicians‚ and industrial professionals working with PowerFlex 753 systems.
Overview of the PowerFlex 753 AC Drive
The PowerFlex 753 AC drive‚ part of the PowerFlex 750 series by Rockwell Automation‚ is a high-performance motor control solution designed for industrial applications. It offers versatile motor control capabilities‚ supporting multiple control methods such as Volts per Hertz‚ Sensorless Vector‚ and Full Vector control. The drive is well-suited for applications requiring precise speed and torque control‚ making it ideal for use in manufacturing‚ material handling‚ and other industrial processes. Its compact design and advanced features‚ including safety functionalities like Safe Torque Off (STO)‚ ensure efficient and safe operation. The PowerFlex 753 is also compatible with EtherNet/IP communication modules‚ enabling seamless integration into industrial networks and advanced control systems. This drive is a reliable choice for machine builders and end-users seeking robust and adaptable motor control solutions.
Importance of the Programming Manual
The PowerFlex 753 Programming Manual is a crucial resource for ensuring the proper setup‚ operation‚ and maintenance of the drive. It provides detailed instructions for programming parameters‚ configuring motor settings‚ and implementing advanced control logic. By following the manual‚ users can optimize the drive’s performance‚ reduce installation time‚ and minimize operational risks. The manual also includes safety guidelines‚ troubleshooting tips‚ and compliance information‚ making it essential for maintaining industrial standards and preventing potential hazards. Engineers and technicians rely on this manual to unlock the full potential of the PowerFlex 753‚ ensuring efficient and reliable operation in various industrial applications; Regular reference to the manual helps users stay updated with best practices and technical specifications.
Target Audience for the Manual
The PowerFlex 753 Programming Manual is primarily designed for engineers‚ technicians‚ and industrial professionals involved in the installation‚ configuration‚ and operation of the PowerFlex 753 AC drive. It is also useful for machine builders‚ system integrators‚ and maintenance personnel who need to understand the drive’s programming and operational parameters. The manual serves as a key resource for both experienced users and newcomers‚ providing detailed guidance on setting up and troubleshooting the drive. Additionally‚ it is beneficial for students and trainees seeking to gain hands-on knowledge of AC drive systems. By following the manual‚ users can ensure safe‚ efficient‚ and reliable operation of the PowerFlex 753 in various industrial applications.
System Architecture and Hardware Overview
The PowerFlex 753 AC drive features a modular design with advanced control capabilities‚ ensuring high-performance motor control and seamless integration with industrial systems. Its robust architecture supports flexible configuration options‚ including EtherNet/IP communication modules‚ and is designed for reliable operation in demanding environments. The drive’s hardware is built to deliver precise speed and torque control while maintaining energy efficiency and safety standards. This section provides an overview of the key hardware components and their roles within the system‚ ensuring users understand the foundational elements of the PowerFlex 753 drive.
Key Components of the PowerFlex 753 Drive
The PowerFlex 753 AC drive comprises essential hardware components designed for high-performance motor control. The primary module includes the drive unit itself‚ which houses the control logic and power electronics. An optional EtherNet/IP communication module enables seamless network integration‚ supporting industrial communication protocols. Additionally‚ the drive features a Safe Torque Off (STO) module‚ ensuring enhanced safety by disconnecting motor torque when required. The Human Machine Interface (HMI) module provides a user-friendly interface for parameter configuration and monitoring. These components work together to deliver precise speed and torque control‚ ensuring efficient and safe operation in various industrial applications. This section highlights the critical hardware elements that make up the PowerFlex 753 drive‚ essential for understanding its functionality and capabilities.
Hardware Installation Requirements
Proper installation of the PowerFlex 753 drive requires adherence to specific hardware guidelines to ensure optimal performance and safety. The drive must be installed in an enclosure with an appropriate NEMA or IP rating to protect against environmental factors. A stable power supply‚ compatible with the drive’s voltage and current ratings‚ is essential. Correct grounding and bonding practices must be followed to prevent electrical noise and ensure safe operation. Mounting hardware should be selected based on the drive’s weight and dimensions‚ and all connections must be securely tightened. Environmental conditions‚ such as temperature and humidity‚ should align with the specifications outlined in the manual. Failure to meet these requirements may result in reduced performance‚ equipment damage‚ or safety hazards. Always refer to the manual for detailed installation instructions and safety precautions.
Compatibility with Industrial Systems
The PowerFlex 753 AC drive is designed to seamlessly integrate with a wide range of industrial systems‚ ensuring compatibility and adaptability in diverse applications. It supports multiple communication protocols‚ including EtherNet/IP‚ making it suitable for networked industrial environments. The drive is fully compatible with Rockwell Automation’s control systems‚ such as Allen-Bradley PLCs and HMIs‚ enabling efficient control and monitoring. Additionally‚ it can operate alongside other industrial devices‚ such as sensors‚ actuators‚ and SCADA systems‚ ensuring holistic system integration. Its modular design allows for easy incorporation into existing infrastructure‚ while its flexible configuration options cater to various industrial automation needs. This compatibility ensures streamlined operations‚ reduced setup time‚ and enhanced performance across industrial applications.
Installation and Setup Guidelines
Ensure proper installation and setup of the PowerFlex 753 drive by following pre-installation checks‚ securing the drive‚ and connecting power and control wiring correctly. Always refer to the manual for specific configuration steps and safety guidelines to guarantee optimal performance and safety.
Pre-Installation Checks and Preparations
Before installing the PowerFlex 753 AC drive‚ perform thorough pre-installation checks to ensure compatibility and safety. Verify the drive’s specifications match the motor and load requirements. Check the power supply voltage and frequency to confirm they align with the drive’s ratings. Ensure all necessary hardware‚ such as mounting brackets and wiring‚ is available and meets Rockwell Automation’s guidelines. Review the installation manual for specific torque and mounting instructions. Properly ground the drive to prevent electrical noise and ensure safe operation. Additionally‚ verify that the environment meets temperature and humidity specifications to maintain performance and longevity. Prepare a clean‚ stable surface for installation to avoid vibration issues. Always follow Rockwell Automation’s safety protocols to prevent accidents and ensure compliance with industrial standards. These steps are crucial for a successful installation and optimal drive performance.
Step-by-Step Installation Process
Mount the PowerFlex 753 drive on a flat‚ stable surface using M6 x 40 bolts‚ ensuring proper alignment. Secure the drive firmly to prevent vibration. Connect the power supply cables to the drive’s terminal block‚ following the wiring diagram in the manual. Wire the motor connections to the output terminals‚ ensuring correct phase sequence. Connect any I/O devices‚ such as sensors or switches‚ according to the system requirements. Power up the drive and verify the display shows normal operation. Configure the drive parameters using the HMI or software tools‚ setting motor parameters‚ speed references‚ and control modes. Test the drive by running the motor at low speed to ensure smooth operation. Finally‚ review all connections and settings to ensure compliance with Rockwell Automation’s guidelines and safety standards.
Power Supply and Wiring Considerations
Ensure the PowerFlex 753 drive is powered by a stable AC supply matching its voltage rating (e.g.‚ 208-230V or 460V). Use appropriately sized cables to minimize voltage drop and ensure reliable operation. Wire the drive’s input terminals according to the manual’s diagrams‚ double-checking phase connections to avoid miswiring. Install an EMI filter if required to comply with industrial noise standards. Ground the drive chassis properly to prevent electrical noise and ensure safety. Use shielded cables for control signals to reduce interference. Follow Rockwell Automation’s guidelines for wiring torque and tightness to maintain secure connections. Always refer to the manual for specific wiring configurations and safety precautions to ensure compliance and reliable performance.
Programming Fundamentals
Programming Fundamentals introduces key concepts for configuring the PowerFlex 753. Learn to set parameters‚ configure motor settings‚ and utilize the HMI for efficient drive control.
Understanding the Programming Parameters
Understanding the programming parameters is essential for optimizing the PowerFlex 753 AC drive’s performance; These parameters define how the drive interacts with motors and industrial systems. Key parameters include speed‚ torque‚ and motor settings‚ which must be configured precisely to match application requirements. The manual provides detailed descriptions of each parameter‚ ensuring proper setup and operation. Parameters are divided into categories like control mode‚ feedback‚ and safety‚ simplifying customization. Rockwell Automation emphasizes adherence to safety standards when adjusting parameters. Incorrect settings can lead to operational issues or safety hazards. Always refer to the manual for guidance on parameter configuration and ensure compliance with industrial regulations. Proper parameter setup ensures efficient‚ reliable‚ and safe drive operation. Regular reviews and updates of parameters are recommended to maintain optimal performance.
Setting Up Motor and Drive Configuration
Setting up motor and drive configuration is crucial for optimal performance and compatibility. The PowerFlex 753 supports various motor types‚ including induction and synchronous motors‚ each requiring specific configurations. Users must select the appropriate control mode‚ such as volts per hertz or vector control‚ based on their application needs. Motor ratings‚ including size and rated current‚ must be accurately set to match the motor specifications. The drive also allows for encoder or sensorless feedback configurations‚ enhancing precision and control. Auto-tuning features simplify motor parameter adjustments‚ ensuring smooth operation. Proper configuration prevents overheating and ensures efficient motor-drive interaction. Always refer to the manual for detailed setup instructions and troubleshooting guidance. Accurate configuration is essential for reliable and efficient operation of the PowerFlex 753 drive system.
Using the Human Machine Interface (HMI)
The Human Machine Interface (HMI) is a user-friendly tool for interacting with the PowerFlex 753 drive. It allows for easy monitoring‚ controlling‚ and programming of drive parameters. Through the HMI‚ users can view real-time data‚ such as motor speed‚ torque‚ and voltage‚ ensuring precise operation. The interface provides intuitive navigation for adjusting settings‚ enabling seamless customization of drive behavior. Key features include parameter editing‚ status monitoring‚ and diagnostic functions. The HMI also supports troubleshooting by displaying fault codes and alerts. With its clear and organized design‚ the HMI simplifies complex tasks‚ making it accessible for both experienced engineers and new users. Always refer to the manual for detailed instructions on HMI setup and operation to maximize its functionality and ensure safe system interaction.
Advanced Programming Features
The PowerFlex 753 offers advanced programming features‚ including customizable control logic‚ enhanced speed and torque regulation‚ and integrated safety functionalities. These features enable precise motor control and adaptability to complex industrial applications‚ ensuring optimal performance and reliability.
Customizing Control Logic and Parameters
Customizing control logic and parameters on the PowerFlex 753 allows users to tailor the drive’s behavior to specific application needs. Through advanced programming‚ parameters such as speed‚ torque‚ and acceleration can be finely tuned. The drive supports customizable logic using Rockwell Automation’s software tools‚ enabling the creation of complex control schemes. Users can define inputs‚ outputs‚ and internal variables to create tailored control algorithms. This feature is particularly useful in industrial environments where precise motor control and synchronization are required. The ability to modify parameters ensures optimal performance‚ efficiency‚ and safety. Additionally‚ the drive’s programmable logic controller (PLC) integration allows for seamless communication with other industrial systems. Customization options are extensive‚ making the PowerFlex 753 highly adaptable to diverse operational demands.
Implementing Speed and Torque Control
The PowerFlex 753 allows precise implementation of speed and torque control‚ enabling users to optimize motor performance for various industrial applications. Through advanced programming‚ users can configure speed and torque parameters to meet specific operational requirements. The drive supports closed-loop control‚ ensuring accurate regulation of motor speed and torque. This feature is particularly useful in applications requiring high precision‚ such as positioning systems or variable-speed pumps. The drive’s software tools provide intuitive interfaces for setting up and adjusting control parameters. Additionally‚ the PowerFlex 753 offers real-time monitoring and adjustment capabilities‚ allowing users to fine-tune performance during operation. This level of control ensures efficient energy use‚ reduced mechanical stress‚ and improved overall system reliability.
Integrating Safety Features
The PowerFlex 753 programming manual emphasizes the integration of advanced safety features to ensure secure operation in industrial environments. The drive supports Safe Torque Off (STO) functionality‚ which safely removes motor torque in emergency situations‚ meeting international safety standards. This feature is critical for protecting equipment and personnel. The manual provides detailed instructions for configuring STO and other safety parameters‚ ensuring compliance with industrial safety regulations; Users can customize safety settings to align with specific application requirements. Additionally‚ the drive’s design includes multiple layers of protection‚ such as fault detection and alarm systems‚ to prevent unexpected shutdowns. By following the manual’s guidelines‚ users can implement robust safety measures‚ ensuring reliable and secure operation of the PowerFlex 753 in various industrial applications. Regular updates and certifications further enhance the drive’s safety capabilities.
Troubleshooting and Maintenance
The PowerFlex 753 manual provides detailed troubleshooting guides‚ diagnostic techniques‚ and maintenance schedules to ensure optimal drive performance and minimize downtime in industrial applications.
Common Issues and Solutions
Common issues with the PowerFlex 753 AC drive include communication errors‚ motor misalignment‚ and incorrect parameter settings. These problems often arise from improper installation or configuration. Solutions typically involve recalibrating the drive‚ verifying network connections‚ and ensuring motor parameters match the connected load. Another frequent issue is overheating‚ which can be resolved by improving ventilation or reducing the workload. Additionally‚ firmware updates may be necessary to address software-related glitches. Regular maintenance‚ such as checking for loose connections and updating settings‚ can prevent many of these issues. Refer to the troubleshooting section for detailed diagnostic procedures and step-by-step solutions to ensure optimal drive performance and minimize downtime.
Diagnostic Tools and Techniques
The PowerFlex 753 AC drive offers advanced diagnostic tools to identify and resolve issues efficiently. The Human Machine Interface (HMI) provides real-time monitoring of drive parameters and fault codes. Rockwell Automation’s software tools‚ such as RSLogix 5000 and Studio 5000‚ enable detailed analysis and troubleshooting. Additionally‚ the drive features built-in status LEDs and alarm codes‚ which indicate specific problems like overcurrent or overheating. Users can also access diagnostic data via the EtherNet/IP module‚ allowing remote monitoring and issue resolution. Regularly reviewing event logs and trending data helps identify potential issues before they escalate. For complex problems‚ Rockwell Automation’s support website and technical forums provide comprehensive guides and solutions. These tools ensure quick identification and resolution of issues‚ minimizing downtime and optimizing system performance.
Regular Maintenance Practices
Regular maintenance is crucial to ensure the optimal performance and longevity of the PowerFlex 753 AC drive. Users should periodically inspect the drive’s enclosure for dust buildup and clean it to prevent overheating. Checking and tightening all electrical connections helps maintain reliable operation. The heat sink should be cleaned to ensure proper cooling‚ and the ventilation system must be clear of obstructions. Firmware updates should be applied regularly to benefit from the latest features and bug fixes. Monitoring the motor and drive parameters through the HMI or software tools can help identify potential issues early. Additionally‚ reviewing the event logs and performing routine backups of drive configurations are recommended. Adhering to these practices ensures the drive operates efficiently‚ reduces downtime‚ and extends its service life.
Network Integration and Communication
The PowerFlex 753 supports advanced network integration‚ enabling seamless communication through EtherNet/IP modules. This facilitates efficient data exchange‚ remote monitoring‚ and control across industrial systems‚ ensuring scalability and reliability.
Overview of EtherNet/IP Module for PowerFlex 753
The EtherNet/IP module for the PowerFlex 753 drive offers robust network communication‚ enabling integration with industrial Ethernet networks. This module supports standard EtherNet/IP protocols‚ ensuring seamless connectivity and data exchange. It allows for real-time monitoring‚ parameter configuration‚ and control of the drive from a central control system. The module enhances scalability and flexibility‚ making it suitable for complex industrial applications. With built-in diagnostics‚ it simplifies troubleshooting and maintenance. Rockwell Automation’s commitment to compatibility ensures the module works effortlessly with existing industrial systems‚ providing a reliable solution for modern manufacturing environments.
Configuring Network Settings
Configuring network settings for the PowerFlex 753 EtherNet/IP module involves assigning IP addresses‚ setting up subnet masks‚ and specifying gateway details. Users can utilize Rockwell Automation’s software tools to streamline this process‚ ensuring proper communication within the industrial network. The module supports DHCP for dynamic IP assignment or static IP configuration for fixed addressing. Security features like firewall settings and VLAN support can also be enabled to protect the drive from unauthorized access. Proper network configuration ensures reliable data transmission‚ minimizing downtime and enhancing overall system performance. Refer to the manual for step-by-step instructions and best practices for configuring network settings tailored to your specific industrial application.
Ensuring Secure Communication
Ensuring secure communication for the PowerFlex 753 EtherNet/IP module is critical to protect industrial networks from unauthorized access and cyber threats. Enable encryption protocols such as AES and TLS to safeguard data integrity. Configure firewalls to restrict access to essential communication ports and implement secure authentication methods like SSH and HTTPS. Regularly update firmware to patch vulnerabilities and maintain compliance with industry security standards; Use virtual local area networks (VLANs) to segregate traffic and monitor network activity for suspicious behavior. Rockwell Automation recommends following best practices outlined in their security guidelines to ensure robust protection. By implementing these measures‚ you can maintain secure communication and prevent potential breaches in your industrial control system.
Safety Considerations and Compliance
The PowerFlex 753 programming manual emphasizes adherence to safety standards and regulations‚ ensuring compliance with industrial safety protocols. It highlights the importance of implementing Safe Torque Off (STO) functionality and provides guidelines for safe installation‚ operation‚ and maintenance practices to protect personnel and equipment.
Understanding Safety Standards for AC Drives
Understanding safety standards for AC drives is critical for ensuring compliance and safe operation. The PowerFlex 753 programming manual aligns with global industrial safety regulations‚ including UL and IEC certifications. These standards address electrical‚ mechanical‚ and functional safety requirements to protect personnel and equipment. The manual emphasizes the importance of proper installation‚ operation‚ and maintenance to meet these standards. It also highlights features like Safe Torque Off (STO)‚ which ensures the drive safely stops motor operation in emergency situations. By adhering to these guidelines‚ users can minimize risks and ensure reliable performance in industrial environments. Always refer to the manual for specific safety protocols and compliance details.
Implementing Safe Torque Off (STO) Functionality
The PowerFlex 753 programming manual provides detailed guidance on implementing Safe Torque Off (STO) functionality‚ a critical safety feature that ensures the drive safely stops motor operation in emergency situations. STO is designed to remove motor torque while maintaining control power‚ preventing unexpected startup or movement. This feature is essential for meeting industrial safety standards and protecting personnel and equipment. The manual outlines step-by-step instructions for configuring STO‚ including parameter settings and wiring requirements. Additionally‚ it emphasizes the importance of testing STO functionality after installation to ensure proper operation. By following the manual’s guidelines‚ users can integrate STO effectively‚ enhancing the overall safety of their industrial systems. Always refer to the manual for specific implementation details and safety considerations.
Compliance with Industrial Safety Regulations
The PowerFlex 753 programming manual emphasizes the importance of compliance with industrial safety regulations to ensure safe and reliable operation. The drive is designed to meet international safety standards‚ such as ISO 13849-1 and IEC 62061‚ providing a robust framework for integrating safety features. The manual guides users through configuring the drive to comply with these standards‚ including risk assessment and safety parameter settings. It also highlights the need to follow proper installation and maintenance procedures to maintain compliance. By adhering to the manual’s guidelines‚ users can ensure their systems meet regulatory requirements‚ reducing potential hazards and legal risks. Compliance is a priority throughout the manual‚ ensuring the PowerFlex 753 operates safely within industrial environments.
References and Additional Resources
For further assistance‚ refer to Rockwell Automation’s official website‚ PowerFlex 753 user manuals‚ technical support‚ and community forums for comprehensive guidance and troubleshooting.
Rockwell Automation Documentation and Support
Rockwell Automation provides extensive documentation and support for the PowerFlex 753 AC drive‚ ensuring users have access to comprehensive resources. The official Rockwell Automation website offers detailed user manuals‚ installation guides‚ and technical notes specific to the PowerFlex 753. These documents are designed to assist with troubleshooting‚ configuration‚ and maintenance‚ ensuring optimal performance. Additionally‚ Rockwell Automation’s technical support team is available to address complex issues‚ while community forums offer peer-to-peer solutions and shared experiences. These resources collectively empower users to maximize the capabilities of the PowerFlex 753 and resolve challenges efficiently.
Online Manuals and Guides
Rockwell Automation offers a wide range of online manuals and guides specifically for the PowerFlex 753 AC drive. These resources are accessible through the Rockwell Automation website and include detailed user manuals‚ programming guides‚ and reference materials. Users can find comprehensive instructions on installation‚ configuration‚ and troubleshooting‚ ensuring seamless integration and operation. The online library also features updated documentation to reflect the latest enhancements and features of the PowerFlex 753. Additionally‚ these guides are organized by topics‚ making it easy for users to navigate and find specific information quickly. This ensures that users can efficiently utilize the full potential of the PowerFlex 753 drive in their industrial applications.
Technical Support and Community Forums
Rockwell Automation provides robust technical support and active community forums for the PowerFlex 753 AC drive. Users can access 24/7 support through the Rockwell Automation website‚ where they can submit tickets‚ chat with experts‚ or call dedicated support lines. Additionally‚ the Rockwell Automation forums offer a platform for users to share experiences‚ ask questions‚ and collaborate with industry professionals. These forums are moderated by experts and often feature discussions on troubleshooting‚ best practices‚ and innovative applications of the PowerFlex 753. Technical support resources also include FAQs‚ knowledge bases‚ and software updates‚ ensuring users have comprehensive assistance whenever needed. This support ecosystem enables users to resolve issues efficiently and stay updated on the latest developments.
Related Posts
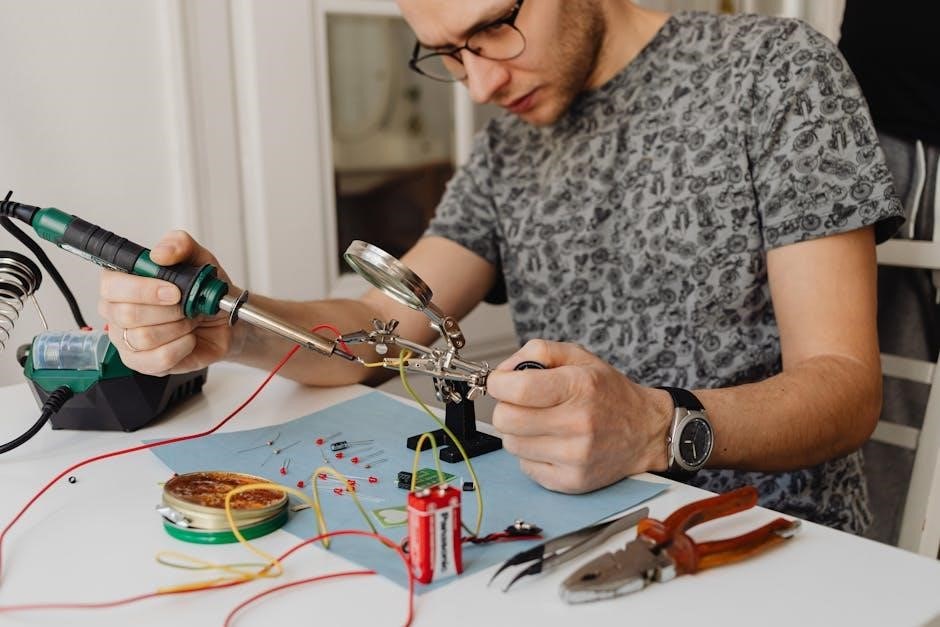
battery tender jump starter manual
Get the most out of your Battery Tender Jump Starter with our comprehensive manual! Learn how to use, charge, and troubleshoot your device effortlessly.
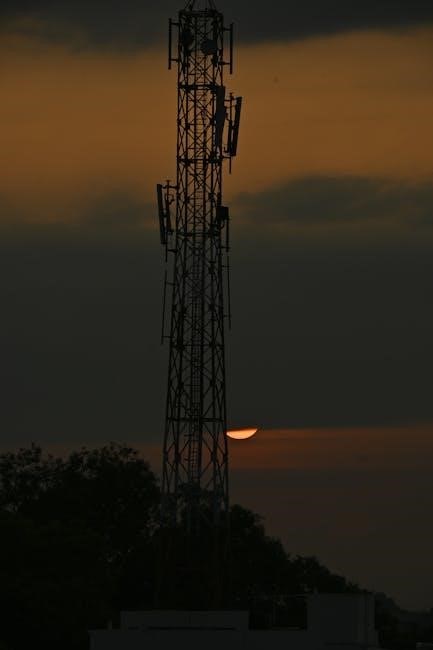
can you get a remote starter on a manual transmission
Discover how to install a remote starter in your manual transmission vehicle safely and efficiently.
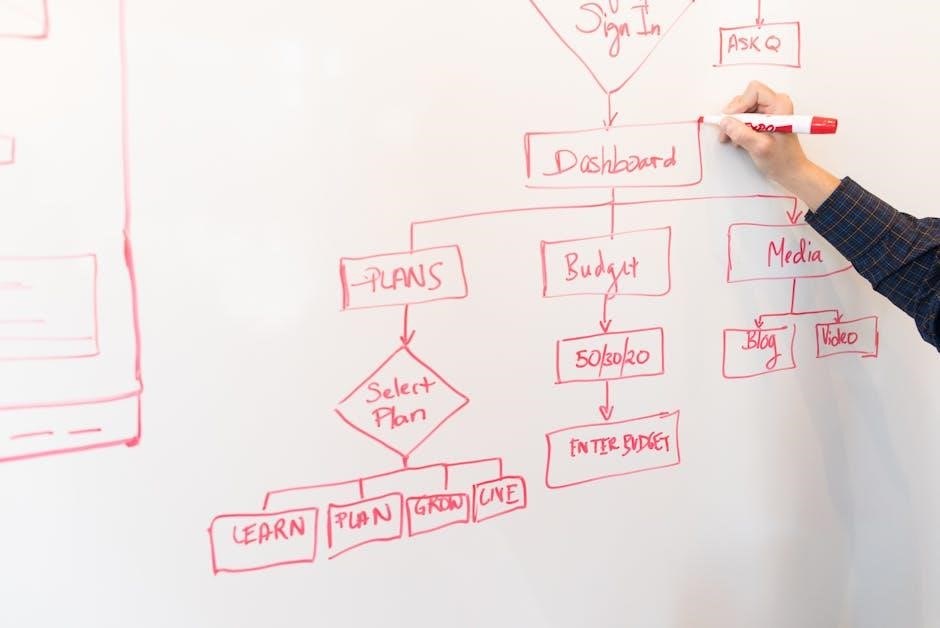
manual swap e46
Learn how to perform an E46 manual swap with our expert guide. Get tips, tricks, and step-by-step instructions for a successful transmission swap. | Jointstuff