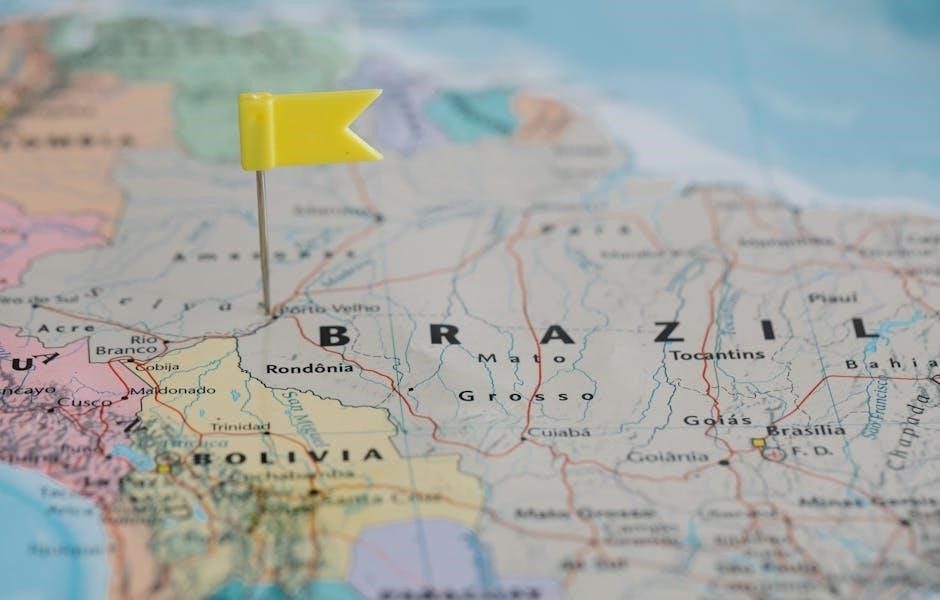
production layout guide
A production layout guide outlines the strategic arrangement of resources, workstations, and equipment to optimize workflow and efficiency, ensuring maximum productivity and safety in manufacturing processes․
1․1 Definition and Importance of Production Layout
Production layout refers to the systematic arrangement of machinery, workstations, and resources within a manufacturing facility to enhance workflow efficiency and productivity․ Its importance lies in minimizing operational costs, reducing waste, and improving safety standards․ A well-designed layout ensures seamless material flow, optimizes space utilization, and supports lean manufacturing principles․ By aligning resources with production objectives, it fosters a structured environment that promotes productivity, employee efficiency, and overall business competitiveness in an ever-evolving industrial landscape․
1․2 Brief History and Evolution of Production Layouts
The concept of production layouts traces back to the Industrial Revolution, where factories first began organizing machinery and workstations to enhance efficiency․ Early layouts focused on basic workflow arrangements, often mimicking craftsmanship rather than standardized processes․
Over time, the introduction of assembly lines by Henry Ford revolutionized production layouts, emphasizing product-specific designs․ Modern layouts now integrate lean principles, modular designs, and smart technologies, reflecting a continuous evolution toward flexibility and efficiency in manufacturing environments․
Key Principles of Production Layout Planning
Effective production layout planning involves aligning resources to enhance workflow, optimize space, and ensure flexibility, ultimately boosting productivity, safety, and cost-efficiency in manufacturing operations․
2․1 Understanding Workflow Processes and Objectives
Understanding workflow processes and objectives is critical for effective production layout planning․ It involves analyzing how materials, information, and tasks flow through the factory to meet production goals․ By mapping out these processes, businesses can identify bottlenecks, inefficiencies, and opportunities for improvement․ Aligning the layout with workflow objectives ensures smooth operations, reduces delays, and enhances overall productivity․ This step is essential for creating a layout that supports both short-term efficiency and long-term business growth․ Proper workflow analysis ensures resources are allocated optimally․
2․2 Maximizing Space Utilization and Resource Allocation
Maximizing space utilization and resource allocation is essential for efficient production․ A well-planned layout ensures that every area of the factory is used effectively, minimizing waste and reducing operational costs․ Poor space management can lead to bottlenecks, congestion, and safety hazards, ultimately affecting productivity․ By optimizing resource allocation, businesses can streamline workflows, enhance worker accessibility, and improve material flow․ This step ensures that the factory operates at its full potential, achieving cost efficiency and higher output without compromising safety or quality standards․
2․3 Flexibility in Responding to Changing Production Needs
Flexibility in production layouts is crucial for adapting to fluctuating demands and product variations․ A modular or scalable design allows businesses to reconfigure workflows and equipment quickly, minimizing downtime․ This adaptability ensures that production can efficiently shift between different product lines or volumes without major overhauls․ Incorporating advanced technologies, such as automation and simulation tools, further enhances flexibility, enabling seamless adjustments to meet changing market requirements and maintain operational efficiency․
Types of Production Layouts
Production layouts include product, process, fixed position, and cellular designs, each tailored to specific production needs, ensuring efficient workflows and resource optimization․
3․1 Product or Line Layout
A product or line layout arranges resources and equipment in a sequential manner to produce a specific product or service․ This layout is ideal for high-volume, standardized production, as it minimizes material handling and reduces production time․ Workstations are positioned along the production line, allowing products to move smoothly from one stage to another․ This design is commonly used in automotive assembly lines, where efficiency and consistency are critical․ It optimizes workflow, reduces costs, and enhances productivity, making it a cornerstone of modern manufacturing processes․
3․2 Process or Functional Layout
A process or functional layout organizes equipment and workstations by similar functions or processes, rather than by product․ This layout is ideal for facilities producing a wide variety of products or requiring frequent changes in production․ It allows for flexibility and efficient use of specialized machinery, reducing downtime and enabling quick adaptation to new production requirements․ Common in industries like food processing, it supports low-volume or custom production, ensuring efficient resource allocation and minimizing production bottlenecks․ This design prioritizes functionality and versatility over sequential workflow․
3․3 Fixed Position Layout
A fixed position layout involves stationary placement of the product, with resources, machinery, and workers moving to the product as needed․ This layout is ideal for large, complex, or heavy products, such as ships or buildings, where moving the product is impractical․ It minimizes transportation costs and is often used in construction or large-scale manufacturing․ The layout requires careful planning to ensure efficient resource allocation and workflow, avoiding bottlenecks and ensuring safety․ It is most effective for low-volume, high-value production scenarios․
3․4 Cellular or Group Layout
A cellular or group layout organizes production into self-contained cells or groups, each handling a specific set of processes or operations․ This layout improves workflow efficiency by reducing material and operator movement․ It is particularly effective for products requiring multiple operations, as it allows for sequential processing within each cell․ Cellular layouts promote lean manufacturing principles, minimizing waste and enhancing productivity․ They are commonly used in machining, assembly, and custom production environments, where flexibility and precision are critical․
Designing an Efficient Production Layout
Designing an efficient production layout involves systematic planning to optimize space, workflow, and resource allocation, ensuring seamless operations and maximizing productivity while minimizing costs․
4․1 Assessing Current Workflow and Identifying Bottlenecks
Assessing the current workflow involves mapping out processes, tracking material flow, and identifying inefficiencies․ Bottlenecks, such as equipment downtime or uneven work distribution, are critical to address․ By analyzing production data and observing operations, businesses can pinpoint areas where workflows are hindered․ Tools like simulation software or lean manufacturing techniques help visualize and resolve these issues․ Regular audits and employee feedback also provide insights into operational challenges․ Addressing bottlenecks ensures smoother production, reduces delays, and enhances overall efficiency, leading to improved productivity and cost savings․
4․2 Creating a Conceptual Layout Design
Creating a conceptual layout design involves visualizing the overall structure of the production area․ It begins with defining business objectives and production goals․ Flowcharts, CAD software, or sketching tools are used to map out potential layouts․ The design should prioritize flexibility, material flow, and space utilization․ By considering workflow patterns and equipment placement, businesses can develop a blueprint that enhances efficiency and reduces operational costs․ This stage ensures the layout aligns with production needs and supports scalability for future growth․
4․3 Detailed Planning and Implementation
Detailed planning and implementation involve translating the conceptual design into actionable steps․ This phase includes assigning specific locations for equipment, workstations, and material storage․ A detailed schedule is created to ensure smooth execution, minimizing disruptions․ Machinery and tools are installed, and employees are trained on the new layout․ Continuous monitoring and adjustments are made to optimize workflow efficiency․ This stage ensures the layout is functional, safe, and aligned with production goals, setting the foundation for long-term operational success․
Tools and Technologies for Layout Optimization
CAD software, simulation tools, and lean manufacturing techniques enhance layout design by streamlining workflows, optimizing space, and improving operational efficiency in production environments․
5․1 Computer-Aided Design (CAD) Software
CAD software is a powerful tool for creating detailed production layouts, enabling precise design and visualization of factory setups․ It allows for 3D modeling of workstations, equipment, and workflows, helping to identify inefficiencies before implementation․ CAD also supports simulation of production processes, ensuring optimal space utilization and resource allocation․ By streamlining the design process, CAD enhances collaboration among teams and facilitates real-time adjustments․ Its scalability and customization features make it an essential tool for modern production layout planning and optimization․
5․2 Simulation Tools for Workflow Analysis
Simulation tools enable detailed analysis and optimization of production workflows, helping to identify inefficiencies and bottlenecks․ These tools allow for virtual testing of layout designs, reducing the need for physical prototypes․ By simulating production processes, businesses can evaluate different scenarios, optimize resource allocation, and improve operational efficiency․ Simulation software also supports employee training and scenario planning, ensuring smoother transitions during layout changes․ This technology is invaluable for predicting outcomes and refining production layouts before implementation, enhancing overall productivity and reducing costs․
5․3 Lean Manufacturing Techniques
Lean manufacturing techniques focus on eliminating waste and optimizing workflows to enhance efficiency․ By applying principles like just-in-time production and standardized work, businesses can streamline their production layouts․ Lean methods identify and reduce non-value-adding activities, such as unnecessary movement or excess inventory․ This approach enables companies to create more agile and adaptable layouts, improving productivity and reducing costs․ Implementing lean strategies ensures a more organized and efficient use of space, aligning with the goals of a production layout guide to achieve sustainable and scalable manufacturing processes․
Case Studies and Real-World Applications
Real-world applications of production layout guides are evident in industries like automotive, food, and textiles, showcasing improved efficiency and productivity through optimized facility designs and workflows․
6․1 Successful Factory Layouts in Automotive Industry
The automotive industry exemplifies effective production layout strategies, with manufacturers like Tesla and Ford optimizing workflows for efficiency․ By arranging workstations and equipment along production lines, these factories minimize bottlenecks and maximize productivity․ Advanced technologies, such as robotic assembly lines and automated material handling systems, are seamlessly integrated to enhance precision and reduce waste․ These layouts not only improve production speed but also ensure worker safety and product quality, setting benchmarks for modern manufacturing excellence․
6․2 Efficient Layouts in Food and Beverage Production
Efficient layouts in food and beverage production are critical for maintaining hygiene, minimizing contamination risks, and maximizing workflow․ Many facilities adopt modular designs, separating raw material storage from processing and packaging areas․ Advanced automation systems streamline operations, reducing manual intervention and ensuring consistency․ For instance, fruit juice factories often use linear layouts to facilitate continuous production, while dairy plants prioritize easy cleaning and sanitation․ These designs enhance productivity, ensure compliance with safety standards, and support sustainable manufacturing practices․
6․3 Optimized Layouts in Textile Manufacturing
Optimized layouts in textile manufacturing focus on streamlining production workflows for efficiency and quality․ Many facilities use fixed position layouts, where machinery is arranged around specific production stages․ Integration of advanced technologies, such as laser marking systems, enhances precision and reduces downtime․ Sustainable practices, like energy-efficient equipment placement, are increasingly prioritized․ These designs minimize material handling, improve worker safety, and ensure consistent product quality․ By adapting to production demands, textile layouts support scalability and long-term operational success․
Future Trends in Production Layout Design
Future trends include integrating smart manufacturing and IoT for real-time optimization, adopting modular layouts for flexibility, and prioritizing sustainability in green factory designs․
7․1 Integration of Smart Manufacturing and IoT
The integration of smart manufacturing and IoT into production layouts enables real-time data-driven decisions, optimizing workflow and resource allocation․ IoT sensors monitor equipment performance, predict maintenance needs, and reduce downtime․ Smart manufacturing systems analyze production data to identify inefficiencies and improve process accuracy․ This connectivity enhances flexibility, allowing layouts to adapt dynamically to production demands․ By leveraging automation and data analytics, manufacturers can achieve higher efficiency, scalability, and sustainability, positioning themselves for future challenges and opportunities in the evolving industrial landscape․
7․2 Adoption of Modular and Flexible Layouts
Modular and flexible layouts are increasingly favored for their adaptability to changing production demands․ These designs allow manufacturers to reconfigure workstations, equipment, and processes easily, minimizing downtime during adjustments․ By using modular components, companies can scale operations up or down based on demand, ensuring efficient resource utilization․ Flexible layouts also enable smoother integration of new technologies and accommodate diverse product lines, making them ideal for industries requiring agility and responsiveness to market changes while maintaining operational efficiency and competitiveness․
7․3 Sustainability and Green Factory Layouts
Sustainability is increasingly integral to modern production layout design, focusing on eco-friendly practices and resource efficiency․ Green factory layouts incorporate natural lighting, renewable energy sources, and waste reduction strategies to minimize environmental impact․ Key elements include energy-efficient equipment, recycled materials, and optimized space utilization to reduce carbon footprints․ Additionally, these layouts often integrate green technologies, such as solar panels and rainwater harvesting systems, to promote sustainability․ By adopting these practices, manufacturers can achieve cost savings, enhance brand reputation, and contribute to global environmental goals while maintaining operational efficiency․
Best Practices for Maintaining an Effective Layout
Regular audits, continuous improvement, and employee training are essential for maintaining an effective production layout, ensuring adaptability, scalability, and efficiency for future growth and performance․
8․1 Regular Audits and Continuous Improvement
Regular audits are crucial for maintaining an effective production layout․ They help identify inefficiencies, bottlenecks, and areas for improvement․ Continuous improvement practices, such as lean manufacturing, enable ongoing refinement of workflows and resource allocation․ By consistently evaluating and optimizing the layout, businesses can enhance productivity, reduce waste, and ensure operational sustainability․ These practices also foster a culture of adaptability, allowing the layout to evolve with changing production needs and technological advancements․
8․2 Training Employees on Layout Optimization
Training employees on layout optimization is essential for maximizing efficiency․ By understanding the principles of production layout design, workers can identify bottlenecks and suggest improvements․ Regular workshops, simulations, and hands-on exercises help staff adapt to changes and implement lean practices․ Empowering employees with knowledge of space utilization and workflow streamlines operations, enhances safety, and fosters a collaborative environment․ Continuous training ensures that the layout remains aligned with production goals and technological advancements, driving long-term productivity and success․
8․3 Adapting Layouts for Scalability and Growth
Adapting layouts for scalability and growth ensures that production facilities can efficiently handle increasing demand or changes in production requirements․ Modular and flexible layouts allow businesses to expand or reconfigure workflows without significant disruptions․ Integrating smart manufacturing technologies and IoT enables real-time adjustments, ensuring optimal resource utilization․ Additionally, incorporating sustainable practices supports long-term growth by reducing environmental impact․ Regular audits and continuous improvement strategies help maintain scalability, ensuring the layout remains responsive to evolving production needs and market demands, fostering resilience and adaptability in dynamic industries․
Related Posts
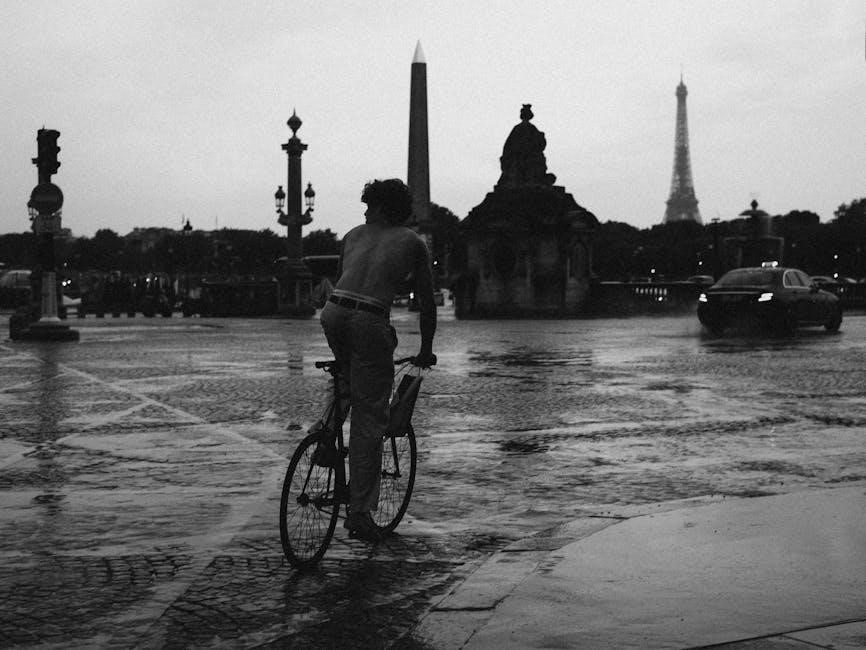
self guided cycling holidays in france
Discover France’s hidden gems with self-guided cycling holidays in France. Enjoy scenic routes, charming villages, and local cuisine at your own pace.
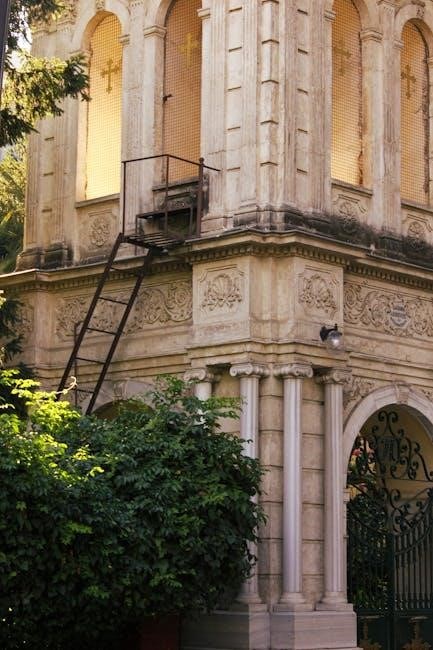
honeywell cross reference guide pdf
Get the Honeywell cross reference guide in PDF. Find compatible parts effortlessly and streamline your workflow.
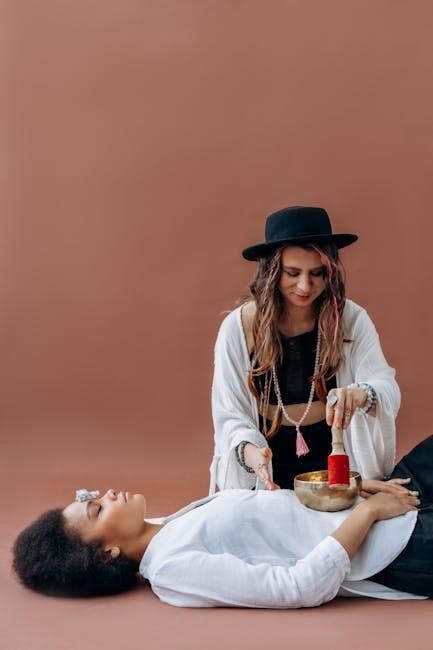
optoma projector user guide
Master your Optoma projector with our comprehensive user guide! Discover setup, troubleshooting, and maintenance tips to enhance your viewing experience.